①ベルトコンベア蛇行検知システム H-BMD
②コルゲートサイロ残量監視システム H-RM
③PH監視システム H-PHM
④混和剤残量監視システム H-AEM
【見回り不要!】生コン工場様、製品工場様
- 悩 み
-
生コン工場、製品工場、砕石工場
工場内装置や施設の監視業務が負担になっている
①ベルトコンベアの蛇行を目視で確認するのが、危険作業となっている。
落鉱した骨材は清掃作業にて撤去しているが、コストと時間がかかるのが不満。
②サイロ上部に登って、目視で残量確認するのは時間がかかる上に、転落事故の危険が伴う。
目視では、骨材の表面が平らでないため正確な残量が判らない。
③排水濃度に異常がないか、担当者が日に何度も施設へ足を運んで数値を確認している。
数値を転記するため手書きとなり、データ管理しにくい。
④混和剤残量確認を忘れて、製造時に不足してしまった。
タンク上部に登って目視で残量確認を行うのが危険作業となっている。
製造計画に基づき必要量を算出しているが、手計算で行うためミスも多く時間がかかる。
- 解 決
-
【見回り不要!】異常発生を検知し事務所へ自動通報
①片寄スイッチで蛇行を検知したら無線で事務所へ通報すると共に、一定値を超えた蛇行の
場合は装置を緊急停止させます。
機器の破損や、火災発生を防ぎます。
②骨材搬入の都度にサイロを昇降しての確認は不要。サイロの骨材残量は2次元センサーが
正確に計測します。
高所での危険作業をなくし、安全で正確な管理を実現します。
③設備の測定値は無線で事務所へ送信。現地での確認作業不要です。
設定した基準値を超えたら、パトライトや警報機で通知します。
④混和剤残量をセンサーで常に測定、事務所でデータ確認可能!
Before
①ベルトコンベアの蛇行確認を目視で行なっているが、
手間がかかる。
狭所や高所の危険作業もあり、神経をつかっている。
蛇行を放置してしまうと落下した骨材が堆積して、
清掃作業等メンテナンスコストが発生してしまう。
蛇行がひどいと、装置が破損する場合もあるので、
現地確認をしない訳にはいかない状況。
②骨材をダンプで搬入のたびに、ドライバーがサイロ
に登って、内部を目視確認するという危険作業に。
サイロ内部は暗く、また骨材の表面も平らでないため、
残量の見間違いをすることも。
③排水濃度に濃度に異常がないか、実際に担当者が日に
何度も設備へ出向き、測定数値の確認を行っている。
測定数値を見て台帳に転記しているので、手書きに
なりデータ管理がしづらい。
④タンクに登って目視で残量確認を行うのが危険作業と
なっている。
事務所からタンク設置場所まで距離があり、残量確認
に手間と時間がかかる。
製造計画から混和剤の必要量を算出しているが、手計
算で行うためミスも多く時間がかかる。
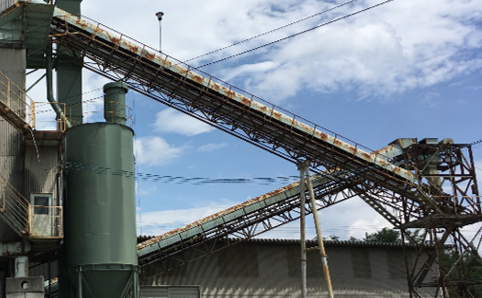
ベルトコンベア

コルゲートサイロ
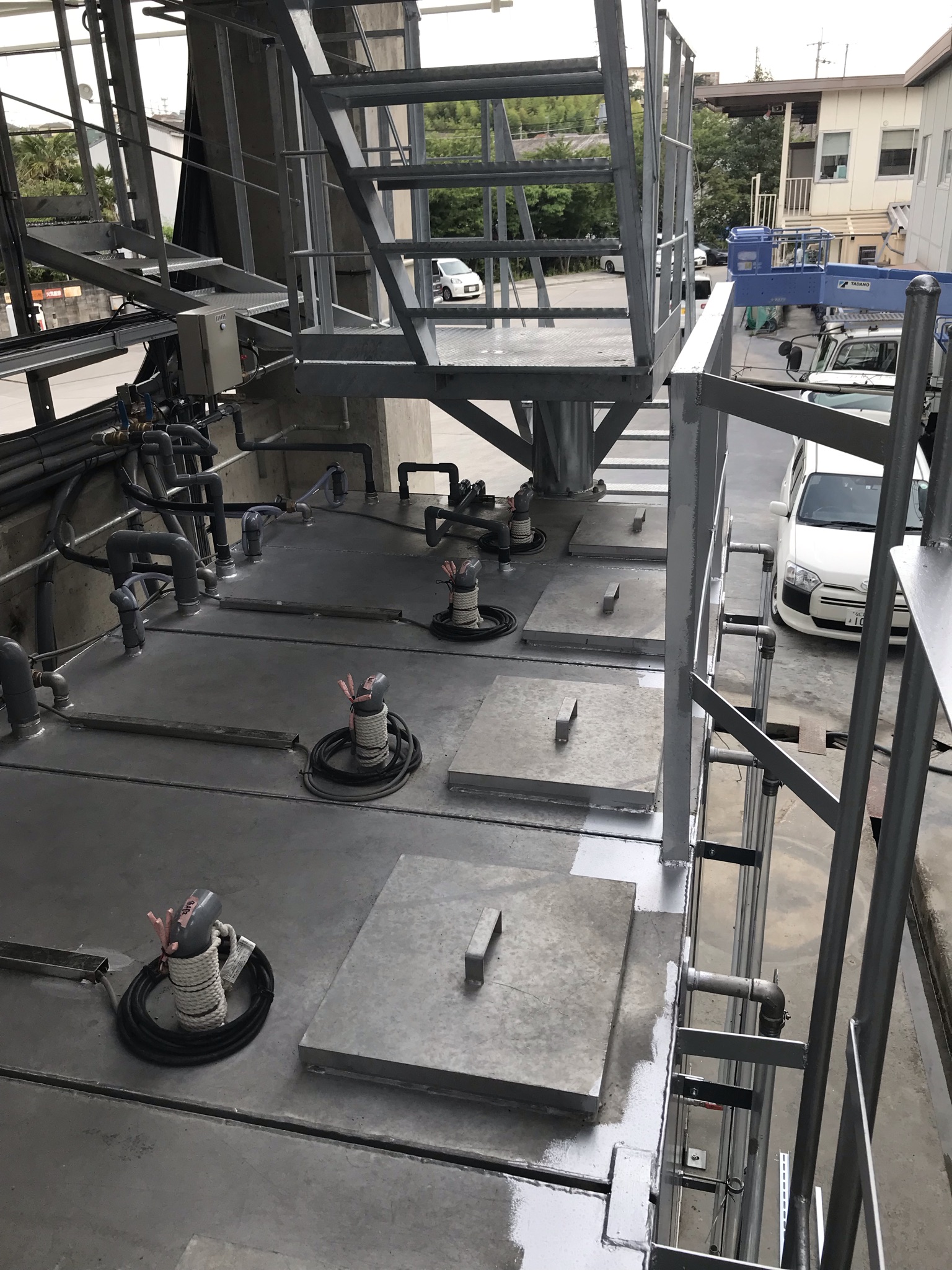
混和剤タンク
After
①現在、最も多く普及しているタイプのベルトコンベアで
は、機構上蛇行を完全に防ぐことはできません。
蛇行の程度が酷くなると、機器の破損や装置のメンテナ
ンスが必要となってしまいます。
自動で蛇行を検知し、通報を無線で事務所へ通知します。
〇ベルト片寄りスイッチをベルトコンベアに設置、ベルト
の蛇行を検知。
〇検知した信号をLoRa無線機で飛ばし、事務所の回転灯
を点灯させてベルトの調整タイミングをお知らせ。
〇一定以上の蛇行が発生した場合は、装置を緊急停止し
ます。
②各骨材サイロの上部に取り付けた2次元センサーが、内
部の隆起・陥没した骨材表面を自動計測し、正確な残量
を表示します。
工場の管理者は事務所にいながら、リアルタイムで残量
が判ります。(屋外モニターで、骨材受入れ地点でも同
じ画面で確認できます。)
骨材搬入のドライバーが、サイロに登り目視するという
一連の作業が不要です。
③PH監視に現地での確認作業は不要です。排水設備の
基準値を超えたら無線で事務所へ通知します。
必要な時だけ現地へ向かえば済むので、不要作業を
削減できます。
④目視での確認作業が不要。TOF方式超小型レーザ距離
センサで液面検出して、正確な残量を検知します。
無線で事務所へ通知し、リアルタイムで正確な残量
確認ができます。
防水・防塵の発信装置を混和剤タンク側に設置、各
タンクの状態を無線で送信。事務所までの配線工事も
不要です。